Use Cases
- TOP
- Use Cases
- Success Story
- Suntory Products Limited
Suntory Products Limited
Supporting Production at the Cutting-Edge Kita Alps Shinano-no-Mori Water Plant!
- Providing No-Code linkage between production facilities and AI fault detection system -
Suntory Products Limited
Summary
The next-generation factory model for Suntory Products began operations in 2021 at the Kita Alps Shinano-no-Mori Water Plant. With its advanced construction, it aims to be “a factory that never stops.” More specifically, in the Suntory Tennensui Kita Alps production line, operating data from various machines are collected in real time, and operation and trends are monitored by the Impulse* AI fault detection system.
*Impulse is a fault detection solution provided by Brains Technology, Inc.
Roughly 80 PLCs are operating within the factory, from various domestic and overseas vendors. Data from the PLCs is collected and transferred to the AI fault detection system via OPC UA communication, using DeviceXPlorer OPC Server (DxpSERVER) and No-Code linkage tool OPC Spider by Takebishi.
<Past issues>
・Predictive fault detection which could not be automatically tasked to threshold monitoring was handled manually. This had the potential for human error.
<Purpose of implementation>
・Eliminate manual predictive fault detection tasks, promote faster fault detection, and aim to improve the operation rate of the facility.
・Allow for data collection settings and other system changes to be implemented by the on-site manager.
Next-Generation factory model that embodies the Smart Factory
Suntory Products plays a central role in the production for the Suntory Group, which is a top-class manufacturing company in the refreshing beverage market. The cutting-edge Kita Alps Shinano-no-Mori Water Plant is located in Omachi, Nagano, and uses the freshest spring water directly from the mountain source to produce Suntory Tennensui Kita Alps Mineral Water.
The state-of-the-art facility was built around the concept of “creating a place which will be loved by our customers, workers, and the surrounding area, using high-level manufacturing and branding to improve efficiency and job satisfaction.” The resulting plant is the embodiment of the Smart Factory, allowing for branded experiences in a space where production coexists with nature.
This is achieved through the proactive utilization of AI technology in the plant. “Data is collected from the equipment and machinery operating on the production line, and AI is utilized to increase the efficiency of fault detection for possible issues which may arise in the facility. Simply put, it aims to increase the productivity of the plant as a whole,” said Hidetaka Okubo, who works in the engineering department of the Kita Alps Shinano-no-Mori Water Plant.
The Tennensui Kita Alps production line contains a wide variety of equipment. According to Mr. Okubo, the production process is as follows. First, mineral water which has been collected from the water source is filtered and purified. Then, plastic bottles produced in the factory are filled and labelled. Finally, the finished bottles are packed in designated amounts, stored, and shipped.
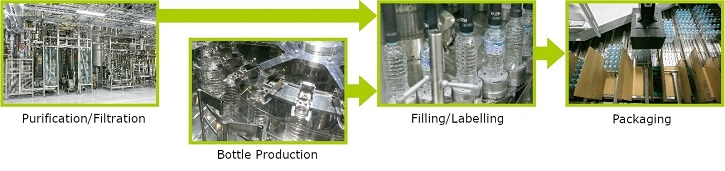
Figure: Tennensui Kita Alps production process
Factories in the past have employed operation monitoring systems (SCADA) to visualize operation status, as well as automated threshold monitoring for fault detection. However, since predictive fault detection could not be handled by threshold monitoring and was addressed manually, undiscovered faults and worker specialization were common issues. To increase the operation efficiency rate through faster and more reliable fault detection, an AI fault detection system was implemented to monitor fault signals to identify trends which separated faulty and normal equipment operation.
That being said, building a perfect AI model takes time. In order to raise the judgement accuracy, the sensor data input into the AI must be added to or changed, and various preprocessing calculations also require testing. This trial-and-error process must be repeated, and using an outside system development company every time the system changes leads to additional delays and costs. As a result, the on-site manager must be able to execute changes to the system on their own.
Linking operation data between the production line and the AI platform
In order to address these problems, Suntory Products implemented Takebishi’s OPC UA communication software DeviceXPlorer OPC Server (DxpSERVER) and No-Code data linkage tool OPC Spider.
“DxpSERVER transmits the data from PLCs, which control all the equipment on the production line, from vendor-specific protocols to OPC UA* communication. OPC Spider obtains the OPC UA equipment data and changes it to a format which is compatible with the cloud-based AI fault detection system before sending the data to the cloud,” Okubo said, giving an overview of the system construction.
*OPC UA is a standard communication protocol in the manufacturing field
Both DxpSERVER and OPC Spider came at the recommendation of the vendor in charge with constructing this system. DxpSERVER is used as a standard OPC server for a wide range of manufacturers, and has a large number of use cases both domestically and overseas.
When considering OPC Spider, Okubo said “we do have an in-house IT department with many skilled experts, but with this implementation we really wanted a system that allowed the on-site manager to implement changes regularly to get better results from the AI system. From that standpoint, we chose OPC Spider because it allowed the various types of data from the plant to be easily defined in a GUI interface and linked to the AI fault detection system.”
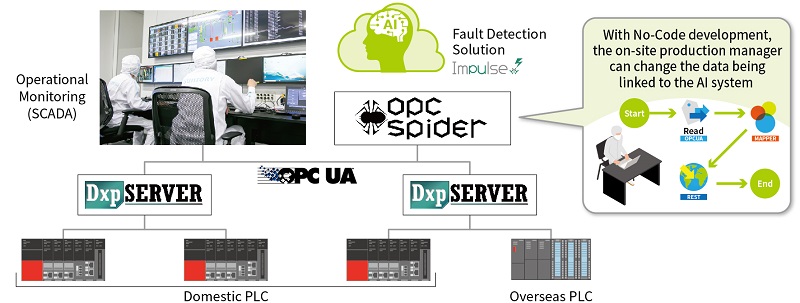
Figure: Impulse AI fault detection system overview
Allowing the on-site manager to focus on valuable improvements to the production line
The AI fault detection system was implemented at the opening of the Shinano-no-Mori Water Plant operations, which allowed the Tennensui Kita Alps production line to be monitored from the start of operations.
“Two years after the construction of the Shinano-no-Mori Water Plant, the equipment has not yet deteriorated. As a result, the system has not been utilized very much. For now, while continuing to experiment, we are slowly expanding the equipment being monitored by the system. By expanding the target machinery, we hope that the on-site manager can work on improving the production line, and reduce the time spent on predictive maintenance tasks.”
AI fault detection system knowhow helps fuel expansion
Mr. Okubo said that it is the company’s aspiration to continue increasing its fault detection accuracy, utilizing the No-Code data linkage benefits of DxpSERVER and OPC Spider to test data which may be useful for the AI model.
The Kita Alps Shinano-no-Mori Water Plant is planning to expand the production line in March of 2023, and is expected to more than double its manufacturing capacity to 330,000,000 cases per year. The importance of the AI fault detection system will undergo a similar expansion.
At the same time, there is consideration of using the insights gained from developing the AI fault detection system in other plants. As the AI fault detection system expands, the whole company will continue the transition towards smart factory integration.

Suntory Products Limited
Kita Alps Shinano-no-Mori Water Plant
Engineering Department
Hidetaka Okubo