Use Cases
- TOP
- Use Cases
- Success Story
- Nittoku Europe GmbH
Nittoku Europe GmbH
Automation Solutions Implemented 3 Months Faster with DxpSERVER
Nittoku Europe GmbH
Summary
Nittoku Europe GmbH (Nittoku Europe) is the Austrian subsidiary of NITTOKU CO., LTD. (NITTOKU), which is known as the leading company in the manufacturing of coil winding machines and winding solutions. The company engages with European manufacturing, and provides comprehensive solutions for its end users in addition to selling their original coil winding machines. To accomplish this, managing the data from surrounding equipment and the conveyer belts is a vital concern.
To manage the equipment data, support for various communication interfaces which correspond to each piece of equipment is necessary. In the past, each of these programs needed to be developed from scratch, which was a slow and costly process. Seeking a solution which could support vendor-specific protocols from a wide range of equipment makers, Nittoku Europe deployed DeviceXPlorer OPC Server (below, DxpSERVER), the OPC supported industrial communication software from Takebishi.
<Past issues>
- Integration of machinery needed to be developed from scratch for each piece of equipment, entailing high development costs and taking a lot of time.
- Connection with host systems such as MES/ERP entailed high development costs and took a lot of time.
- With long implementation times, adding value to winding machines and other systems was difficult.
<Purpose of implementation>
- Smooth system integration for a wide variety of equipment, reducing the development costs required for connection.
- Reduced the development costs required to connect with the host system (such as MES/ERP) of the end user.
- Able to focus on the core business of maximizing the capability and functionality of winding machines.
The critical role of DxpSERVER in the automated solutions of Nittoku Europe
DxpSERVER is an integral part of the Turnkey and Automated Winding Solutions offered by Nittoku Europe. In addition to acting as a data bridge between the line control system and the Nittoku Special Controllers (NCs) installed on the coil winding machines on the production line, DxpSERVER can also communicate with the surrounding equipment and conveyers on the customer-side.
Nittoku Europe CEO Richard Werkl explained that “within the line control system, DxpSERVER facilitates the production instructions for each piece of equipment, monitors the operation mode and status of the manufacturing components, sends error messages, pre-set values, value limits, and provides feedback on other performance metrics for all aspects of the line control system. In addition, for the turnkey automation solutions implemented by Nittoku Europe, the solutions must be linked with the customers conveyer belts as well as the surrounding equipment. DxpSERVER is a huge help in this area as well.”
Mr. Werkl went on to say that “the processing parameters and sensor information for the control data is collected for traceability management, and DxpSERVER is also sometimes used to connect with related systems such as MES or ERP.”
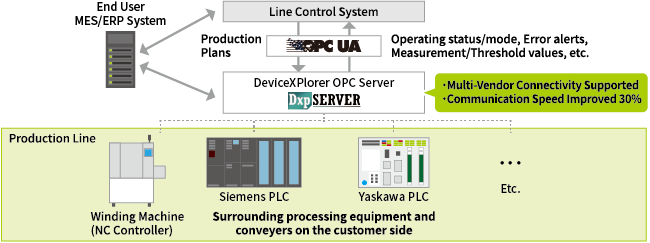
Figure: Nittoku Europe Automated System
Communication Performance and Technical Support were the deciding factors
Nittoku Europe began testing OPC servers to reduce development costs and increase productivity. Peter Santner spoke about the implementation, saying, “the first thing that stood out about DxpSERVER was that it supported standard protocols such as Modbus/TCP and BACnet, as well as the vendor-specific protocols for PLCs, machine controllers, robots, and processors, all with a simple connection process. In other tests, DxpSERVER had communication speeds 30-50% faster than other products, which led to improved performance.”
In addition, Mr. Werkl said that the quality of technical support also played a significant factor in their decision: “When we had a problem accessing some of the data during the implementation, the Takebishi support team was dedicated to analyzing the problem and quickly applying an appropriate solution to fit our needs, ensuring that the problem was solved.”
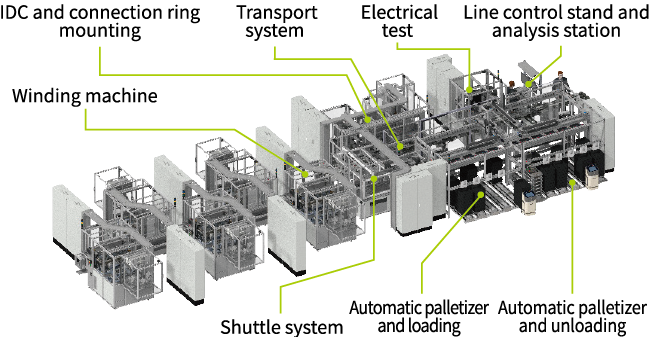
Figure: Nittoku Winding Machine and surrounding equipment
System Deployment period reduced by 3 months
Since Nittoku Europe implemented DxpSERVER in 2018, they have deployed automated winding solutions in the production line of their customers at a rate of roughly 15 per year.
With DxpSERVER, Nittoku Europe is able to smoothly integrate their line control system into the existing machinery, greatly reducing the lead time from initial planning to the start of operation of the customer’s production line. Mr. Werkl was happy to report that “the construction period has been reduced by 3 months” since the implementation of DxpSERVER.
With DxpSERVER contributing to reduced system integration times, Nittoku Europe is considering further expansion of their operations. According to Mr. Werkl, “we are currently working mainly with customers in the automotive and medical fields, but plan to expand into other fast-growing industries in the future as we continue to widen the range of our automated solutions for our customers.” With a wider client base, they are expecting to expand the annual number of systems constructed and integrated for their customers from their current pace.
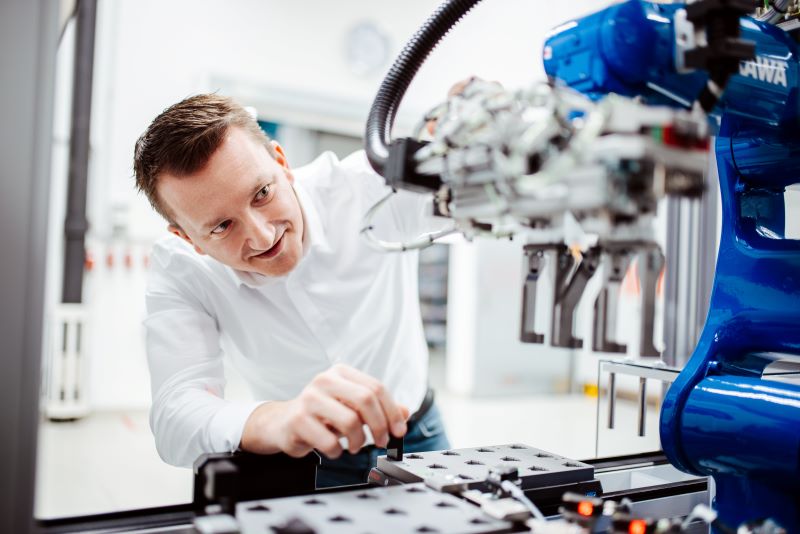
Dipl. Ing.
CEO
Richard Werkl
Head of Electrical &
Software Engineering
Peter Santner